|
|

|
Tecnica
: I segreti
del motore a scoppio |
|
|
|
|
Valvole,
condotti di aspirazione e scarico |
|
|
|
Le
valvole sono organi meccanici adibiti all’apertura e chiusura
di sezioni di passaggio per l’afflusso di gas dal condotto di
aspirazione al cilindro e dal cilindro al condotto di scarico.
Sono comandate tramite alberi a camme in testa o tramite
meccanismi ad aste e bilancieri (più antiquati e meno
utilizzati oggi).
Efflusso
dei gas attraverso la valvola
Le
valvole nel loro moto mettono a disposizione dei gas una sezione
di passaggio di area variabile. Le condizioni di efflusso
attraverso la valvola costituiscono un fenomeno piuttosto
complesso perché in prossimità del fungo della valvola stessa
i gas subiscono una forte deflessione causa di irreversibilità
e turbolenze.
Un'analisi
accurata può essere condotta con codici numerici di simulazione
della gasdinamica tridimensionale o tramite sperimentazione con
tecniche di visualizzazione quali l'anemometria laser. Al
motorista più spesso interessa poter definire dei parametri
globali che sintetizzino i complessi fenomeni in gioco e
forniscano delle utili indicazioni in fase di progettazione.
Per
questo quella che di solito viene definita è la "permeabilità"
del complesso valvola‑sede o della testata del motore nel
suo insieme, cioè l'attitudine della valvola a far fluire una
portata di gas tra due ambienti a pressione diversa. La
permeabilità viene misurata sui cosiddetti banchi
di flussaggio che possono essere schematizzati come in
figura.
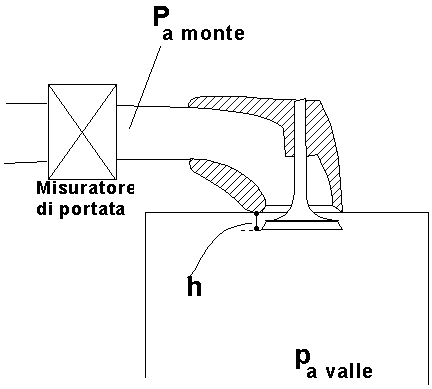
|
Figura
1: Elementi costituenti un banco di flussaggio. |
La
testata viene collegata, da un lato con un ambiente in cui regna
la pressione totale
(cioè in condizioni stazionarie) e dall'altro con un ambiente a
pressione
(dove il fluido è
in moto) e la portata massica di aria viene misurata per diverse
posizioni dell'alzata valvola h, cioè dello spostamento in direzione assiale dalla posizione
di riposo. Se durante la misura l’alzata della valvola è
costante, si parla di banco di flussaggio stazionario, se invece
la valvola è mantenuta in movimento dall’albero a camme,
l’apparecchiatura si chiama banco di flussaggio instazionario
o dinamico. La portata così misurata viene confrontata con la
portata che fluirebbe in condizioni isentropiche attraverso un
ugello di sezione "equivalente". Tale ugello non è
però definito in modo univoco: alcuni ricercatori assumono come
ugello equivalente quello di area pari all'area della sezione
normale del condotto in corrispondenza della valvola (p/4.dM), altri invece scelgono l'area della superficie cilindrica con
diametro di base pari al diametro massimo della valvola ed
altezza uguale all'alzata valvola (p.
dM.h)
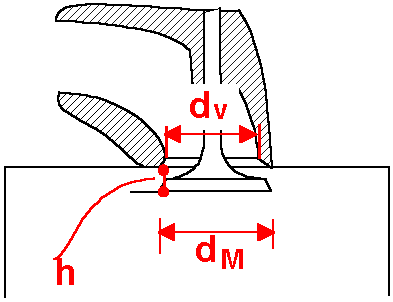
|
Figura
2: Particolare delle grandezze geometriche
caratteristiche della sezione del condotto in
prossimità della sede valvola. |
La
differenza fondamentale quindi tra le due convenzioni risiede
nell'aver scelto una sezione di riferimento costante nel primo
caso e variabile con l'alzata nel secondo.
Il
rapporto tra la portata misurata e la portata ideale di
riferimento genera un coefficiente adimensionale che viene
chiamato coefficiente di
efflusso. Il coefficiente di efflusso ottenuto utilizzando
la prima delle due portate di riferimento (quella con un'area
costante) verrà indicato con
Cd nel
seguito, mentre quello ottenuto utilizzando la seconda (area
variabile con l'alzata) verrà indicato con
Cdf.
|
|
|
|
|
Andamento
del coefficiente
Cdf al
variare dell'alzata delle valvole
Il
coefficiente di efflusso
Cdf ha qualitativamente
l'andamento di figura al variare del rapporto alzata
valvola/diametro del condotto:

|
Figura
3: Andamento qualitativo del coefficiente di efflusso;
caso di valvola di aspirazione (moto dal condotto al
cilindro).
|
Per alzate piccole il flusso è ben guidato ma gli attriti sulle
superfici bagnate sono preponderanti e l'area effettiva di
passaggio è minore dell'area presa come riferimento;
All'aumentare dell'alzata gli attriti hanno un peso
decrescente mentre il flusso si mantiene relativamente ben
guidato;
In corrispondenza di alzate maggiori la forte deflessione
subita dal flusso causa una contrazione della vena
ed un aumento considerevole delle dissipazioni.
|
In pratica l'area va moltiplicata per un fattore riduttivo
circa pari a
, in cui
è
la metà dell'angolo al vertice del cono della valvola.
|
|
|
|
|
Fattori
che influenzano il coefficiente di efflusso
Nelle
figure che seguono sono riportati gli andamenti del coefficiente
di efflusso
Cdf
ottenuti sperimentalmente al variare di alcuni fattori, quali:
-
Angolo
al vertice del cono valvola.
Le
figure qui di seguito mostrano il
Cdf in funzione del
rapporto alzata/diametro valvola
h/dM
per due
diversi angoli al vertice del cono della valvola
2.q supponendo di
mantenere costante il rapporto
s/dM tra l'altezza della
sede e il diametro della valvola (vd. figura).
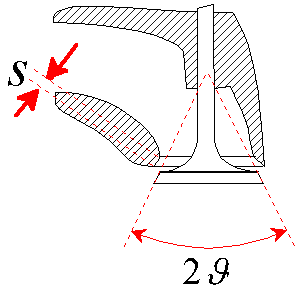
|
Figura
4: Definizione di angolo del cono e di spessore s
della sede valvola.
|
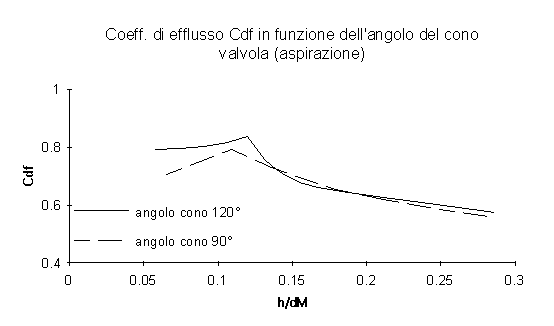 |
Figura
5: Coefficiente di efflusso Cdf al variare del
rapporto alzata/diametro della sede valvola per due
diversi valori dell’angolo del cono (moto dal
condotto al cilindro). |
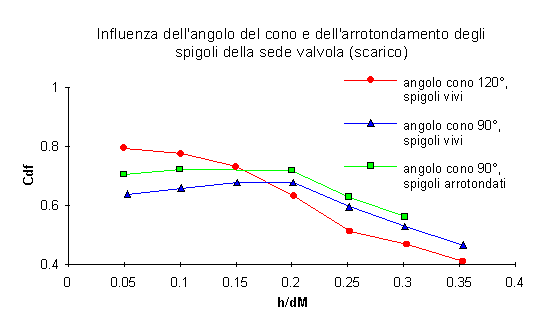 |
Figura
6: Coefficiente di efflusso Cdf al variare del
rapporto alzata/diametro della sede
valvola per due diversi valori dell’angolo del cono
e per due configurazioni della sede valvola (moto
dal cilindro al condotto).
|
Alle
piccole alzate il coefficiente di efflusso
Cdf
è leggermente più
elevato quando l'angolo di apertura del cono è grande (120°)
perché l'area effettiva di efflusso cresce circa secondo
quando
h/dM è piccolo.
All'aspirazione, al crescere dell'alzata valvola il coefficiente
di efflusso non dipende più dall'angolo
q, mentre allo scarico le maggiori aperture del cono risultano
penalizzanti a causa della flessione della vena fluida che non
è più guidata bene. E' da notare anche l'interesse ad
arrotondare tutti gli spigoli della sede valvola.
- Raggio
di curvatura del condotto in prossimità della valvola
La
figura che segue presenta due diverse configurazioni del
condotto in prossimità della valvola. A sinistra è riportata
una configurazione in cui il raggio di curvatura del condotto è
piccolo e quindi si ha un "gomito" relativamente
stretto in prossimità della valvola; nella configurazione di
destra il raggio di curvatura è invece più ampio. Le prove
sperimentali confermano quanto suggerito dall'intuizione: il
coefficiente di efflusso
Cdf
è più elevato nel
caso di ampi raggi di curvatura del condotto e migliora
ulteriormente se si riduce la strozzatura in corrispondenza del
supporto della guida valvola. L'andamento è simile sia che si
tratti di valvole di aspirazione con flusso dal condotto al
cilindro, sia che si considerino valvole di scarico in cui il
flusso è dal cilindro al condotto. La strozzatura dovuta al
supporto valvola è ineliminabile: in sua assenza la valvola
avrebbe flessioni dovute alle forze generate dai gas di scarico.
E’ necessaria una corretta progettazione della guida per
evitare eccessive turbolenze nel moto del fluido.
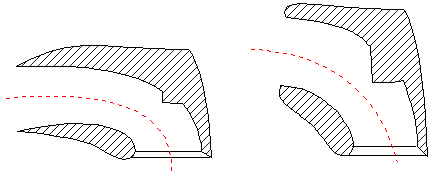 |
Figura
7: Il raggio di curvatura del condotto in prossimità
della valvola ha una forte influenza sulle perdite di
carico in tale area: il condotto della figura di
sinistra provoca perdite superiori al condotto di
destra. In quest’ultimo la sede della guida valvola
non risulta ottimizzata in quanto si protende
eccessivamente nel condotto costituendo un ostacolo al
flusso dei gas. |
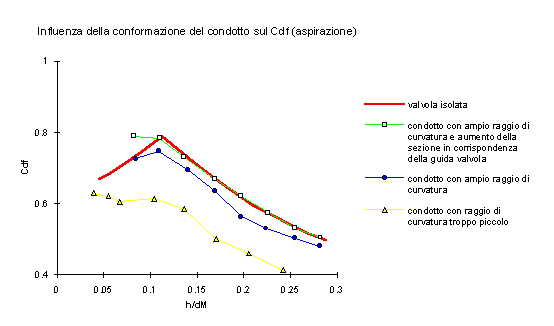 |
Figura
8: Influenza della conformazione del condotto in
prossimità della valvola (moto
dal condotto al cilindro).
|
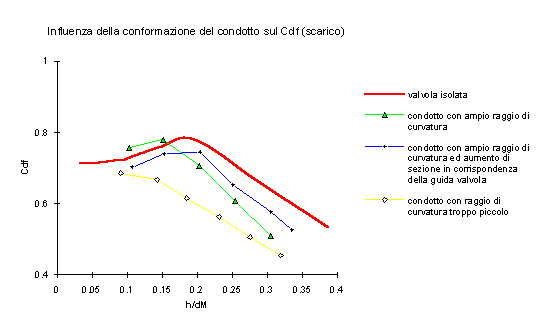 |
Figura
9: Influenza della conformazione del condotto in
prossimità della valvola (moto
dal cilindro al condotto).
|
Le
valvole di aspirazione sono più grandi e in numero maggiore
(per motori plurivalvole) di quelle di scarico perché una
perdita di carico del fluido all’aspirazione compromette la
capacità del motore di dare lavoro. Questo è più gravoso nei
motori diesel dove il carico, ovvero la quantità di coppia o
potenza richiesta non è regolato da una valvola a farfalla che
dosa la portata d’aria ma dalla quantità di combustibile
iniettato. In tali motori, detti “ad accensione spontanea”,
la combustione è data dall’elevata pressione dell’aria in
ingresso che genera l’accensione spontanea della miscela
aria/combustibile: tanto maggiori saranno le perdite di carico
in termini di pressione, tanto minore sarà la pressione nel
cilindro e tanto più difficoltosa sarà la combustione.
D’altro canto elevate perdite allo scarico provocano
un’eccessiva contropressione: ovvero durante il moto di
risalita il pistone può incontrare una resistenza eccessiva da
parte dei gas.
|
|
|
|
|
Area
della sezione efficace
L'area
della sezione efficace è definita

Ed
è l’area che avrebbe la sezione di efflusso se, a parità di
portata, tutto il processo avvenisse reversibilmente. Essa è
facilmente calcolabile ad ogni posizione angolare quando è nota
la legge di alzata della valvola. L'integrale della curva
dell'area efficace tra gli angoli di apertura e di chiusura
fornisce una valutazione della permeabilità del sistema
considerato, cioè della sua attitudine a far fluire una portata
sotto salti di pressione prefissati.
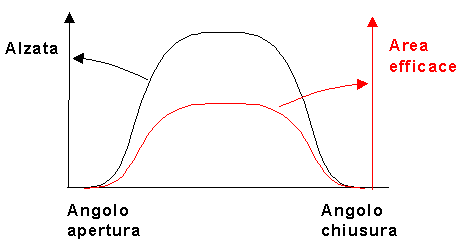 |
Figura
10: Curva di alzata valvola e andamento dell’area
efficace in funzione dell’angolo di rotazione
(andamento qualitativo). |
|
|
|
|
|
Fasatura
delle valvole
La
fasatura delle valvole in un motore a 4 tempi, cioè la scelta
degli angoli di apertura e chiusura delle valvole, è un aspetto
dal quale dipendono molte delle caratteristiche del motore
stesso. La sua ottimizzazione è un processo che va di pari
passo con l'ottimizzazione dei condotti di aspirazione e scarico
la cui geometria influisce fortemente su tutto il processo di
sostituzione del fluido di lavoro, fenomeno quest’ultimo
tipicamente instazionario.
Quanto
più un motore è destinato a funzionare a regimi elevati, tanto
più è importante che le aree delle sezioni equivalenti di
aspirazione e scarico siano elevate e che la permeabilità del
sistema sia elevata per evitare strozzature e perdite di carico
eccessive. Per questo, compatibilmente con l'insorgere di
fenomeni collaterali indesiderati, si cercherà di aumentare
quanto più possibile la durata angolare delle fasi di
aspirazione e scarico.
Gli
angoli che definiscono la fasatura sono (vd. Figura
):
1.
AAS: angolo di Anticipo
dell'Apertura dello Scarico
(ingl EO: exhaust open) misurato a partire dal PMI,
2.
RCS: angolo di Ritardo
della Chiusura dello
Scarico (ingl. EC:
exhaust close), misurato a partire dal PMS,
3.
AAA: angolo di Anticipo
dell'Apertura dell'Aspirazione
(ingl IO: intake open), misurato a partire dal PMS,
4.
RCA: angolo di Ritardo
della Chiusura dell'Aspirazione
(ingl IC: intake close), misurato a partire dal PMI.
|
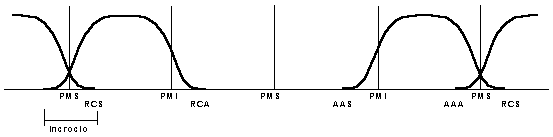
|
Figura
11: Tipico andamento delle leggi di apertura delle
valvole di aspirazione e scarico. Sono evidenziati gli
angoli di apertura e chiusura di ciascuna valvola e la
loro posizione rispetto al Punto Morto Superiore (PMS)
e al Punto Morto Inferiore (PMI).
|
Gli
angoli di fasatura della distribuzione vengono generalmente
indicati partendo dal PMS durante la fase di incrocio
(contemporanea apertura di aspirazione e scarico).
Su una vettura “tranquilla” si potrà avere una
fasatura 10-50-50-10 (rispettivamente per RCS, RCA, AAS, AAA).
su un’autovettura più sportiva una fasatura
30-70-70-30 e
su
autovetture da competizione con elevati regimi di funzionamento
una 50-90-90-50.
Nel
primo caso l'incrocio dura soltanto 10+10 gradi di rotazione
dell'albero a gomiti (da AAA a RCS), mentre nell'ultimo il
periodo di contemporanea apertura delle valvole di aspirazione e
scarico dura ben 50+50 gradi.
La
scelta dell'angolo AAS è operata principalmente minimizzando la
somma del lavoro perso in espansione e del lavoro perso durante
la risalita del pistone per la presenza di una pressione nel
cilindro superiore alla pressione atmosferica. Come mostra la Figura
che si riferisce ad un motore Diesel, un anticipo
eccessivo causa una elevata perdita di lavoro di espansione ma
anche una diminuzione del lavoro di espulsione dei gas combusti.
Viceversa un anticipo insufficiente permette di raccogliere un
maggior lavoro durante l'espansione ma la risalita del pistone
avviene quando la pressione nel cilindro è ancora
eccessivamente elevata.
|
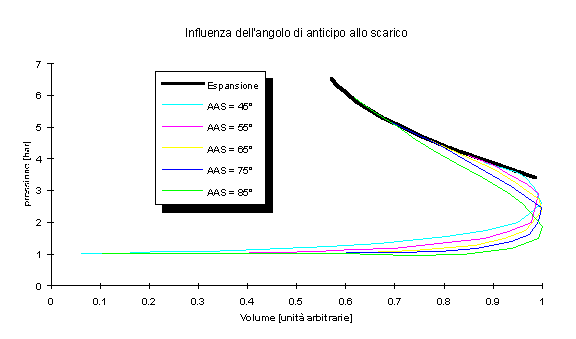 |
Figura
12: Influenza dell’angolo di anticipo allo scarico (AAS)
sulla pressione nel cilindro e quindi sul lavoro di
pompaggio.
|
La
figura che segue mostra che la somma delle perdite per
interruzione dell'espansione e per espulsione dei gas combusti
alla risalita del pistone (prima parte del lavaggio) ha un
minimo in corrispondenza dell'angolo AAS ottimale (curva
superiore); le perdite e il valore dell’angolo AAS ottimale
diminuiscono quando aumentano le dimensioni della valvola e
quando viene ottimizzato il progetto del condotto di scarico in
prossimità della valvola; in tal caso infatti lo scarico
spontaneo ha una minor durata angolare. Per lo stesso motivo,
un'ulteriore sensibile diminuzione delle perdite e dell'AAS
ottimo si verifica al diminuire del regime di rotazione.
|

|
Figura
13: Andamento del lavoro perso al variare
dell’angolo AAS in quattro diverse configurazioni.
|
I benefici dell’angolo di incrocio sono connessi allo
sfruttamento della depressione che si crea nel cilindro alla
fine della fase di scarico a causa dell’inerzia della colonna
dei gas combusti. Durante questa fase l’ingresso della carica
fresca è così favorito dalla fuoriuscita dei gas caldi verso lo
scarico. Poiché l’inerzia dei gas è maggiore ai regimi elevati
mentre il tempo disponibile per il ricambio del gas diminuisce
al crescere del regime, l’angolo di incrocio tende ad aumentare
nei motori destinati a funzionare ad elevati regimi. Si noti
però che, alle basse velocità di rotazione, un incrocio elevato
può portare alla fuoriuscita della carica fresca attraverso la
valvola di scarico (con conseguente diminuzione del rendimento
ed aumento delle emissioni di inquinanti se la carica fresca
aspirata contiene anche il carburante). E’ possibile sfruttare
l’apertura delle valvole per generare una leggera
sovralimentazione, che porta ad un benefico riempimento del
cilindro (maggiore è la quantità d’aria aspirata, maggiore è il
lavoro che il motore è in grado di dare): all’apertura della
valvola di aspirazione viene generata un’onda di espansione che
si muove dalla valvola al filtro di aspirazione, ovvero l’onda
“risale la corrente. L’onda di compressione così generata si
muove verso la valvola e, se perviene alla sezione terminale del
condotto quando la valvola è ancora aperta, si ottiene un
beneficio sul riempimento. Si potrebbe mostrare che il beneficio
è massimo quando il ritorno avviene in corrispondenza delle
massime alzate della valvola, cioè a metà circa della fase di
aspirazione.
Nella
realtà il fenomeno è più complesso di quanto qui descritto
perché le onde si propagano in un mezzo (il gas) non in quiete
ma perturbato dal passaggio di onde precedenti. Tuttavia quanto
qui qualitativamente illustrato mantiene la sua validità.
L’effetto così ottenuto viene detto “accordo in
aspirazione”.
Per
ottenere un buon
accordo all'aspirazione in un intervallo più elevato di regimi
sono attualmente piuttosto diffusi svariati sistemi in cui
vengono modificati gli angoli di fasatura della distribuzione al
variare della velocità di rotazione del motore (sistemi
di distribuzione a fasatura variabile) e/o la geometria dei
condotti di aspirazione (sistemi
di distribuzione a geomteria variabile).
Sistemi
di distribuzione a fasatura variabile.
Poiché
generalmente si interviene sulla fasatura delle sole valvole di
aspirazione, tali sistemi sono caratterizzati dall’avere
alberi a camme separati per aspirazione e scarico. Si possono
individuare due famiglie:
a) Sistemi in cui l'albero a camme di aspirazione può
essere sfasato rigidamente al raggiungimento di un prefissato
regime di soglia. In questo modo è possibile aumentare il RCA
(e diminuire della stessa quantità l'AAA) ai regimi più
elevati in modo da meglio sfruttare i consistenti effetti
inerziali.
|
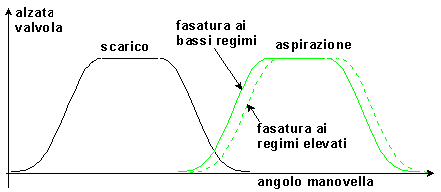
|
Figura
14: Principio di funzionamento di alcuni sistemi a
fasatura variabile.
|
b) Sistemi in cui, al raggiungimento di un regime
prefissato, il profilo di alzata delle valvole passa da una
configurazione ottimizzata per i bassi regimi ad una più adatta
ai regimi elevati. Tali dispositivi, che a seconda del
costruttore assumono denominazioni diverse (VVT‑Variable
Valve Timing, CPS‑Cam Profile Switching, ecc.) sono
caratterizzati da un’intrinseca maggiore flessibilità dei
precedenti perché, oltre che sulla fase è possibile
intervenire sul’intera legge di alzata.
Sistemi
di distribuzione a geometria variabile.
Un
altro accorgimento spesso adottato per ottenere gli stessi
benefici consiste nel modificare la lunghezza dei condotti di
aspirazione al variare del regime in modo da mantenere fasato il
ritorno dell'onda di compressione con l'istante di massima
apertura della valvola di aspirazione.
I
due accorgimenti, fasatura variabile e geometria variabile,
posso anche essere adottati contemporaneamente. I benefici che
si ottengono in termini di riempimento e coppia sono
significativi ed attualmente giustificano l'adozione di tali
dispositivi su motori di classe medio‑alta nonostante
l'incremento di costo e la maggior complessità costruttiva (con
i problemi di affidabilità che possono derivarne).
|
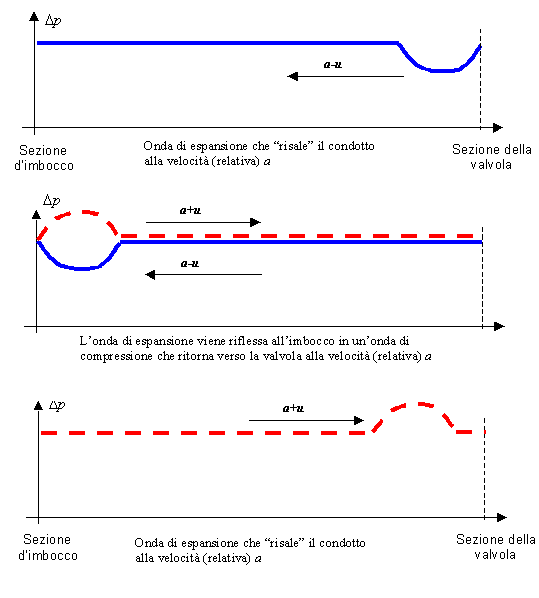
|
Figura
15:
Schema di propagazione delle onde nel condotto di
aspirazione.
|
|
|
|
|
|
|
|
Tutti i marchi appartengono ai legittimi proprietari. Non si intende
ledere alcun Copyright.
Se pensi che i tuoi interessi siano stati colpiti scrivici. |
|